Product Model
hgpl-40-20-a-b
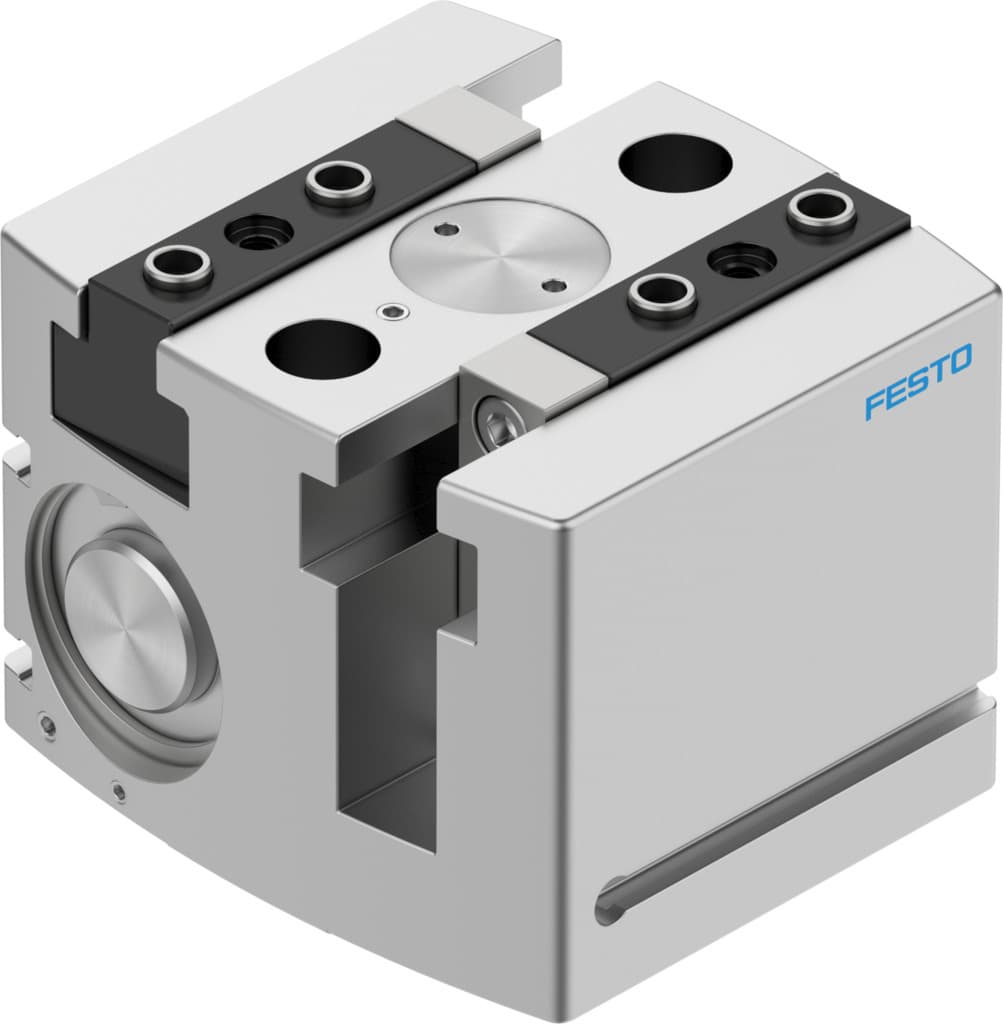
Selling Points
- 1High Precision Handling: The HGPL-40-20-A-B gripper ensures maximum replacement accuracy of less than 0.2 mm and angular backlash of less than 0.2 degrees, making it perfect for precise handling tasks.
- 2Versatile Operation: This double-acting parallel gripper can operate in any position, providing flexibility in various industrial applications. Its twin piston design ensures smooth operation and high precision.
- 3Robust Construction: Built with hardened steel gripper jaws and smooth-anodized aluminum housing, the HGPL-40-20-A-B offers robust construction and durability. It is also RoHS compliant, ensuring environmental safety.
- 4Efficient Performance: With a gripping force of 1038 N (opening) and 1216 N (closing) at 6 bar, this gripper provides efficient performance in handling various materials. The operating pressure range is from 3 to 8 bar, ensuring optimal performance in different conditions.
- 5Easy Integration: The HGPL-40-20-A-B gripper is designed for easy integration with Festo's pneumatic systems. It supports position detection via proximity switch, making it simple to integrate into existing automation setups.
Technical Specifications
Detailed engineering parameters based on manufacturer documentation
Parameter | Value | Parameter | Value |
---|---|---|---|
Size | 40 | Stroke per gripper jaw | 20mm |
Max. interchangeability | 0.2mm | Max. gripper jaw angular play ax, ay | 0.2deg |
Max. gripper jaw backlash Sz | 0.05mm | Rotational symmetry | 0.2mm |
Pneumatic gripper repetition accuracy | 0.03mm | Number of gripper jaws | 2 |
Actuator system | Pneumatic | Mounting position | Any |
Mode of operation | Double-acting | Gripper function | Parallel |
Gripping force backup | Without | Structural design | Twin piston Guide Piston gate valve T-shape Gear rack/pinion |
Position sensing | For proximity sensor | Symbol | 00991894 |
Operating pressure | 3bar 8bar | Max. operating frequency of pneumatic gripper | 1Hz |
Min. opening time at 6 bar | 190ms | Min. closing time at 6 bar | 180ms |
Max. mass per external gripper finger | 420g | Operating medium | Compressed air as per ISO 8573-1:2010 [7:4:4] |
Information on operating and pilot media | Operation with oil lubrication possible (required for further use) | Corrosion resistance class (CRC) | 2 - Moderate corrosion stress |
LABS (PWIS) conformity | VDMA24364-B1/B2-L | Ambient temperature | 5°C 60°C |
Gripping force per gripper jaw at 6 bar, opening | 519N | Gripping force per gripper jaw at 6 bar, closing | 608N |
Mass moment of inertia | 27.6kgcm2 | Maximum force on gripper jaw Fz, static | 2500N |
Maximum torque on gripper jaw, Mx static | 125Nm | Maximum torque on gripper jaw, My static | 80Nm |
Maximum torque on gripper jaw, Mz static | 100Nm | Relubrication interval for guidance elements | 5MioCyc |
Product weight | 2560g | Type of mounting | With internal thread and centering sleeve Via through-hole and centering sleeve |
Pneumatic connection | M5 | Note on materials | RoHS-compliant |
Housing material | Wrought aluminum alloy, smooth-anodized | Gripper jaw material | Hardened steel |
Manufacturer ID | 3361487 |
Specifications may be subject to change without notice