Product Model
150-F480NCRD
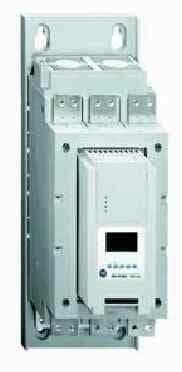
Selling Points
- 11. High Performance and Efficiency: The Allen-Bradley 150-F480NCRD delivers consistent performance in various industrial applications. Its ability to smoothly accelerate and decelerate three-phase motors reduces mechanical stress, thereby increasing the lifespan of the motors.;
- 22. Advanced Diagnostics and Control: Equipped with sophisticated diagnostics, this motor controller ensures high performance and efficiency. The built-in LCD and keypad or PC software setup facilitate process optimization, making it easier to monitor and control motor operations.;
- 33. Robust Design for Demanding Tasks: Designed to handle demanding tasks, the 150-F480NCRD can control heavy-duty motors with ease. Its maximum output current of 480A and 400 HP power output make it suitable for a wide range of industrial applications.;
- 44. Efficient Heat Dissipation: The open enclosure design of the 150-F480NCRD facilitates easy access for maintenance and effective heat dissipation. With a heat dissipation rate of 290 W, it prevents overheating even under severe loads, ensuring reliable operation.;
- 55. Versatile Installation Options: The compact size of the 150-F480NCRD (290 mm wide, 276.5 mm deep, and 600 mm tall) makes it suitable for various installation locations without compromising on power or functionality. Its weight of 45.8 kg ensures durability in tough industrial settings.
Technical Specifications
Detailed engineering parameters based on manufacturer documentation
Parameter | Value | Parameter | Value |
---|---|---|---|
Weight Unit | KG | Stock Status | NON_STOCKED |
Dimension Length | 0.0 | Dimension Width | 0.0 |
Lead Time | 20 | Dimension Height | 0.0 |
Quick Turnaround | false | Preferred Availability | false |
Repairable | REPAIRABLE | Metal parts construction | Plated brass, copper or painted steel |
Control modules construction | Thermoset and thermoplastic moldings | Enclosure | Open type |
Number of poles | 3 | Line/load side power terminals | Two M12 x 1.75 diam holes per power pole |
Control terminals | ClAing yoke connection, M3 screw clA | Power terminal markings | NEMA, CENELEC EN50 012 |
Function | Single direction | Internal bypass | Yes |
Break | 360VA for auxiliary contacts | Make | 3600VA for auxiliary contacts |
Vibration | Opsal: 1.0 G peak, 0.15 mm (0.006 in) displacement | Power pole construction | Heatsink hockey puck thyristor modular design |
Height | 600 mm (23.62 in) | Depth | 276.5 mm (10.89 in) |
Width | 290 mm (11.42 in) | Shock | Opsal: 5.5 G |
Weight | 34.915 | Pollution degree | 2 |
Altitude | 2000 m | EMC immunity levels | Surge transient: per EN/IEC 60947-4-2 |
EMC emission levels | Radiated emission: Class A | Protection against electrical shock | IP2X (with terminal covers) per IEC for power circuit |
Operating temperature | Open: -5 to 50 °C (23 to 122 °F) | Humidity | 5...95% (noncondensing) |
Storage and transportation temperature | -20 | Steady state heat dissipation with control and fan power | 290 W |
Contact type | Auxiliary contacts 19/20 (Aux #1), 29/30 (Aux #2), 31/32 (Aux #3) and 33/34 (Aux #4) | Input ON-state current | 20mA @ 120V AC/40mA @ 240V AC, 7.6mA @ 24V AC/DC for control circuit |
Rated operational current | 3A @ 120V AC, 1.5A @ 240V AC for auxiliary contacts | Input ON-state voltage, min | 85V AC @ 19.2V DC/20.4V AC for control circuit |
Input OFF-state voltage, max | 50V AC @ 10V DC/12V AC for control circuit | Reset resistance | 1600 ? ± 100 ? for PTC input ratings |
Response resistance | 3400 ? ± 150 ? for PTC input ratings | Short circuit trip resistance | 25 ? ± 10 ? for PTC input ratings |
Allen bradley power supply control module, min | 1606-XLP50E @ 24V DC (-15%, +10%) | Tachometer input | 0...5V DC @ 4.5V DC = 100% Speed |
Cold resistance of PTC sensor chain, max | 1500 ? for PTC input ratings | Transient time control module | 500 ms @ 24V DC (-15%, +10%) |
Inrush time control module | 250 ms @ 24V DC (-15%, +10%) | Response time | 800 ms for PTC input ratings |
Voltage at PTC terminals (RPTC = 4 kΩ), max | <7.5 for PTC input ratings | Steady state watts control module | 24 W @ 24V DC (-15%, +10%) |
Transient watts control module | 60 W @ 24V DC (-15%, +10%) | Voltage at PTC terminals (RPTC = open), max | 30V for PTC input ratings |
Inrush current control module | 5A @ 24V DC (-15%, +10%) | Number of sensors, max | 6 for PTC input ratings |
Short circuit protection device performance (SCPD) type | Type 1 | Integrated motor overload protection | Yes |
Rated control supply voltage at DC | 24 V | Optional controller feature | SMB smart motor braking control: provides motor braking without additional equipment for applications that require the motor to stop quickly, braking current is adjustable from 0...400% of the motorâs full-load current rating |
Standard available fault current, max | 70kA @ 690V for maximum FLC | Standard controller feature | Status indication: stopped, starting, stopping, at speed, alarm and fault |
Utilization category | MG 1 per UL/CSA/NEMA for power circuit | Type of contacts | Progmable NO/NC for auxiliary contacts |
Type of control circuit | Electromagnetic relay for auxiliary contacts | Conventional thermal current (Ith) | AC/DC: 5 A for auxiliary contacts |
Type of current | AC for auxiliary contacts | High capacity available fault current, max | 69kA @ 600V, maximum current 800 A time delay Class J or Class L fuse for line connected motors |
Number of contacts | 1 for auxiliary contacts | Short-circuit protection device list | Standard fuse, circuit breaker and high capacity time delay class CC/J/L |
Input OFF-state current | <10 mA AC, <3 mA DC for control circuit @ input OFF-state voltage | Rated operational voltage | 200...600V AC (-15%, +10%) per UL/CSA/NEMA for power circuit |
Insulation voltage | Rated 500V per IEC for power circuit | Transient protection | Metal oxide varistors: 220 J (optional) for power circuit |
Ampere tested north american style, max | A070D33xxx1250 A100URD73xxx1250 @ 690V for maximum FLC | Ampere tested european style, max | 9 URD 73xxx1250 6,6URD33xxx1250 @ 690V for maximum FLC |
Delta connected motor current | 277...831A @ 500/575V AC, 3-phase | Line connected motor current | 160...480 A @ 600/Y/690V AC, 3-phase |
Dielectric withstand | 2500V per IEC for power circuit | Rated impulse voltage | 6000V per IEC for power circuit |
Delta connected motor power, max | 900Hp @ 575V AC, 60 Hz, 3-phase | Line connected motor power, max | 600Hp @ 600V AC, 60 Hz, 3-phase |
Operating frequency | 50/60 Hz for power circuit | Repetitive peak inverse voltage rating | 1600V per UL/CSA/NEMA for power circuit |
DV/DT protection | RC snubber network for power circuit | Heatsink fan rating | 60VA @ 110/120V AC or 220/240V AC |
Transformer control module | 75VA @ 100...240V AC (-15%, +10%) | Trip current rating | 117% of motor FLC |
Trip classes | 10, 15, 20 and 30 | Control options | Brake control |
Controller type | Soft starter | Overload current for delta connected devices | 277 A |
Overload current for line connected devices | 160 A | Rated control supply voltage at AC 60 Hz | 24 V |
Rated control supply voltage at AC 50 Hz | 24 V | Rated operating voltage Ue | 200 |
Voltage type for actuating | AC/DC | With display | Yes |
Product Family | SMC Flex | Controller Rating | 480 A 200-400Hp @ 460V AC |
Control Voltage | 24V AC/DC |
Specifications may be subject to change without notice